Seguro que, de pequeño, te cargaste unos cuantos de estos platos pese a su fama de irrompibles. En los setenta eran color ámbar o color verde (aunque también existían modelos transparentes, más antiguos) y en todas las casas había, mínimo, una de estas vajillas que llenaban la casa de pequeñísimos fragmentos más o menos cúbicos si, por lo que fuera, estallaba uno de sus platos, vasos, tazas o fuentes, que se han seguido fabricando y están disponibles hoy aún en muchos más colores. Ahora, después de casi 80 años de historia –la empresa se fundó en 1945- la última fábrica de Duralex, situada en la francesa ciudad de Orleans, echa el cierre por culpa, se supone, de los precios del gas.
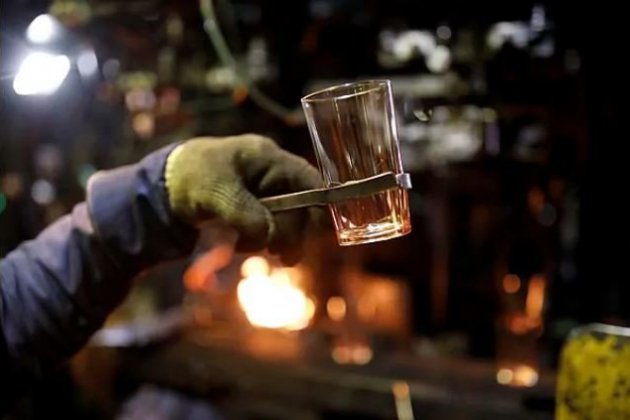
¿Por qué duraban tanto?
Al vidrio de las vajillas Duralex se le aplicaba un tratamiento especial que consistía en aplicarle, justo después de que se acabase de moldear, calor suficiente para hacerle alcanza una temperatura de entre 600 y 700 grados. Cuando se llegaba a ese límite, se sometía al material a un enfriamiento muy rápido que le otorgaba una resistencia a los impactos dos veces superior a la del vidrio convencional. El nombre de estos platos, conviene recordarlo, procede de un principio del derecho romano Dura lex, sed lex (la ley es dura, pero es la ley) que se combina con el concepto metalúrgico de ley, que define el porcentaje de metal puro que existe en una aleación. Así, las vajillas Duralex son aquellas que, por la composición y el tratamiento del vidrio que las componen, resultan ser las más duras y eso, casi, se ha asumido como ley durante prácticamente un siglo. El sistema que permitió fabricar estos platos fue aplicado, primerom por Saint Gobain y se concibió para mejorar la durabilidad de los cristales de los coches, pero luego, a partir de 1945, se aplicó a las vajillas. Por eso, porque la técnica es la misma, unos y otras se fragmentan en trozos minúsculos cuando se rompen o, mejor dicho, estallan. Ahora, una parte de esta historia tecnológica podría perderse.
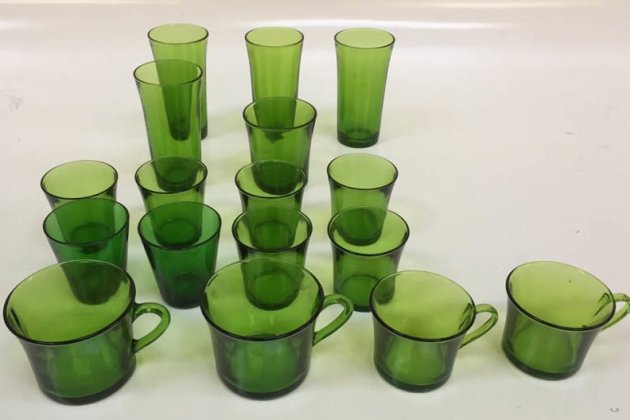
Uso intensivo de gas
El calentamiento de la masa vítrea que permite fabricar los platos se realiza, claro, utilizando el mismo gas que, en los últimos meses, ha visto incrementar su precio con la misma rapidez casi que se debe emplear para acometer el enfriamiento súbito que otorga al Duralex su característica resistencia. Así, el 1 de noviembre se detiene la producción de la última fábrica de la marca, situada en Orleans, aunque hay esperanzas de que sea sólo momentáneamente. Durante medio año, la empresa se dedicará a vender los productos que tienne en stock y los 250 empleados de la planta se irán al paro. Hoy, el coste del gas ha pasado de suponer un 7% del gasto total que exigen realizar la fabricación de un plato de Duralex a representar un 46%. En abril, si la cosa mejora, valorarán volver a producir pero, de momento, Duralex echa el cierre.